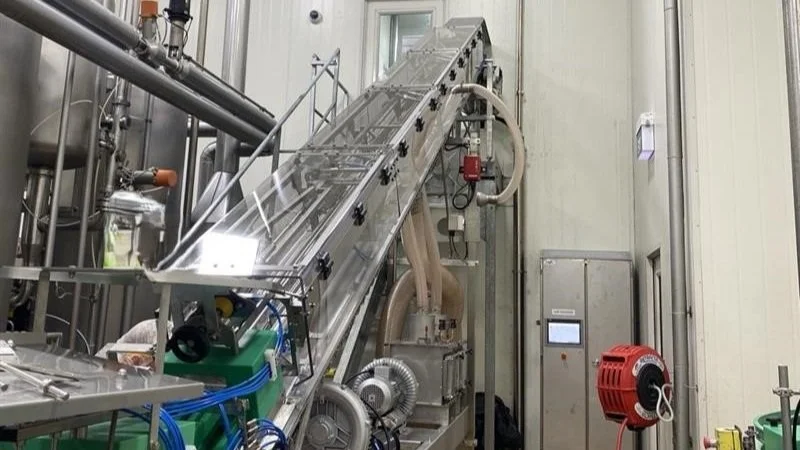
Production Line Air Rinser
Overview
TPG Projects recently executed the " Empty Can Inspection" project, enhancing quality control for a prominent beverage client. This initiative involved the installation of an advanced inspection system on the Ferrum can line, designed to detect dirt and minute deformities in cans, thereby reducing potential quality issues and unplanned downtime.
Project Scope
The project implemented a high-speed empty can inspection system to improve reliability in detecting defects before the filling process. This system, compatible with both current and future can formats, ejects defective cans without affecting line efficiency, ensuring sustained quality and operational continuity.
Key Benefits
-
Enhanced Quality Control
The system provides an additional layer of quality assurance by identifying and ejecting faulty cans early.
-
Operational Efficiency
By preventing faulty cans from reaching the filling stage, the system reduces unplanned downtime and improves production line uptime.
-
Data-Driven Insights
The inspection equipment logs data on can defects, facilitating early detection of trends and enabling proactive quality improvements.